ENERGY
POWER GENERATION
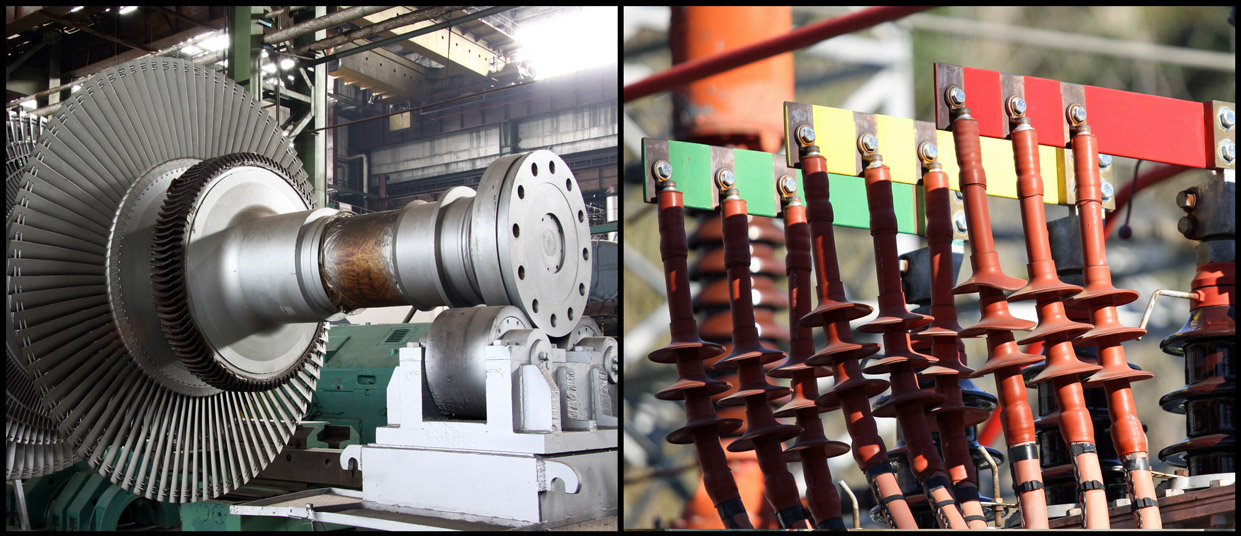
APPLICATIONS
- EReduction of electrical contact resistance
- EImproved wear resistance
- EIncreased corrosion resistance
- EPre-brazing surface preparation
- EAnti-seizure
- ESurface hardness
- EBetter brazeability
- EBearing Fit
- EImproved electrical conductivity, contact, aluminum bus bars with silver plating
- EResizing bearing spans
- ERehabilitation of sleeve seats
- ERepair of crankshafts and crankshaft diameters
- EAutocatalytic Nickel Retention Tank Repair
- EBearing Housing Repair, Rotor Shafts and Generator
- ESwitch Resizing turbine shaft couplings, turning diameters, bearing journals and turbine wheels
- ERepair of seat, disc and needle defects
COMPONENTS
- ESilvering of the blades
- EShock absorbers
- EWedges
- EShaft coatings and engine components
- EBearings of wind turbine bearings
- EWind turbine slip rings
- EGear Boxes
- EDiesel engines
- ERetention tank
- EGenerators
- ETurbines
- EValves
MOTORS & GENERATORS
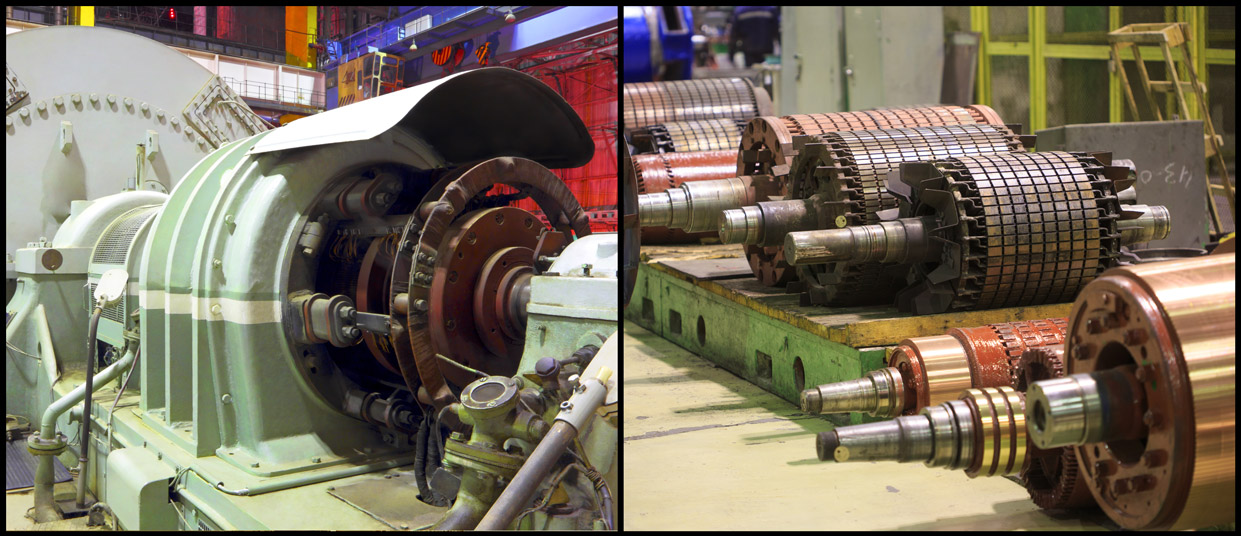
The main areas concerned are the bearing surfaces (motor flange) and wheel bearing wedges on turbine shafts.
APPLICATIONS
Selective electrochemical metallization of a worn bearing surface is faster and more efficient than dressing or thermal spraying processes.
DC motors and generator slip rings produce copper oxide films that reduce electrical conductivity and cause arcing and pitting especially during start-up of a stalled motor. Excessive deterioration is observed in highly corrosive environments, such as bleaching of pulp and paper mills. Deposition of a layer of 2.5μ (0.0001 in.) Of rhodium, then a layer of 1.3μ (0.00005 in.) Of gold on the switch, allows to space the frequencies of maintenance and prolong the service life.
WIND TURBINES
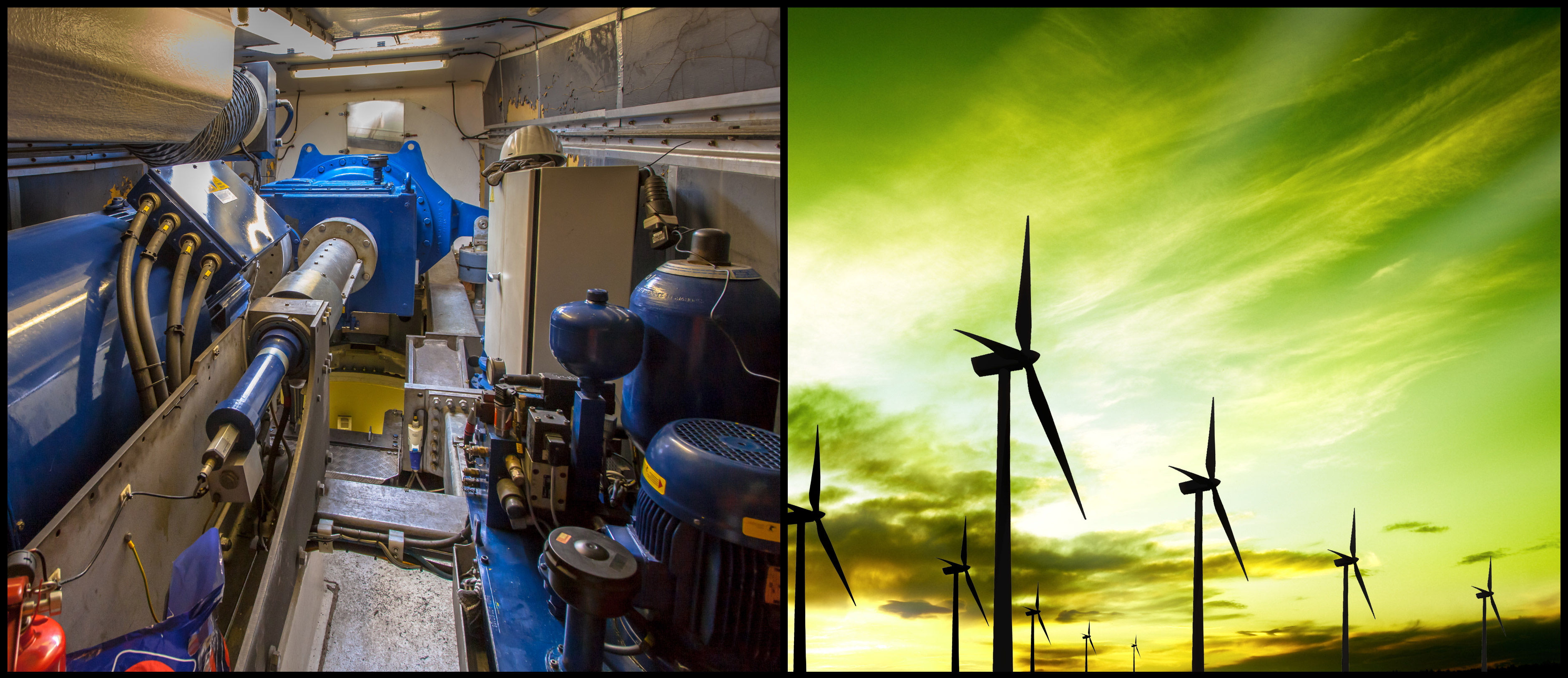
The first wind farms have reached a phase of their useful life requiring the rebuilding or replacement of drive shafts, bearing and gear systems for the repair of engines and generators. Kaytek CSP has realized the only reconstruction of the worn section of a wind turbine drive shaft in Canada; the metallization was carried out with a more durable metal than the original one. This operation, however, required the dismantling and transportation of this component to our facilities to be rebuilt.
On-site reconstruction or repair without dismantling
Kaytek CSP is currently developing the system that will enable direct machining and electrochemical metallization work with a portable combined system to be performed directly in the wind turbine tower.
This system will be operational in the fall of 2019.
APPLICATIONS
- ETurbine shafts
- EGear Boxes
- EBearing Housing